|
 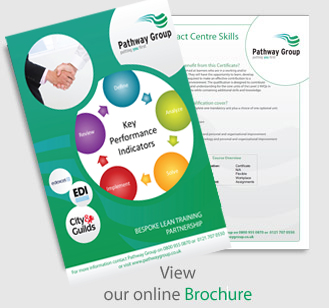 |
Apply for this Course (Lean Training Partnership) |
|
|
|
|
More about Bespoke Lean Training
|
|
Bespoke Lean TrainingThe course is aimed at people from all industries across all levels and everyone can benefit from the course. It will be tailored to suit the specific company needs. We will teach some lean tools and techniques to help make your business more profitable, improve the quality or reduce lead times, through the elimination of waste, to give your employees some ownership, pride and empowerment within your organisation. The QualificationLearning will take place through a company specific, 6 hour training session. We will teach the tools and techniques needed and help you to apply them to your organisation. We will aid the process through weekly visits to ensure that you get the most out of the experience. The course is assessed by yourselves. We will look at current Key Performance Indicators (KPIs), at the inception of the course, make some improvements and revisit the same KPIs after eight weeks have elapsed. Entry QualificationNo prior attainment necessary. Course DurationThe improvement will take eight weeks to complete. The time and effort that you put into that period will determine the results Course FormatThis qualification compromises of 2 pathways - Process Improvement or Quality Improvement. From the chosen pathway you willcomplete all the mandatory units plus the required number of optional units. 56 credits must be achieved. How it all WorksTools and Techniques Used | Brief Summary | Workplace Organisation | Consider the work area and its activity and determine where information, materials, tools and/or equipment are missing, or require a new location and where improvements to the area or activity could be made. | Visual Management | This involves identifying the appropriate parts of the process or work area that will have visual controls and identifying the key performance indicators which are to be displayed in the work area. | Flow Process Analysis | We use the principles and procedures of flow process analysis within a given work area to produce a flow process analysis sheet. We identify and categorise elements of waste, and problems or conditions within the process and make recommendations where improvements can be made. You will use the information gathered to evaluate and prioritise the opportunities for improvements. | Problem Solving Techniques | We identify the nature and extent of the problem and obtain all the relevant information relating to it, using appropriate problem solving tools and applying them within a team focused environment. | Creating SOP's | This will involve gathering information of the method used when performing the operation/process. You will list the preparations required from start to finish, the quality and safety standards to be maintained, the drawings, tooling, fixtures, gauges, and other items that are used during the operation or process. | Set Up Reduction Techniques | It involves carrying out the principles and processes of set-up reduction on a machine or process set-up, a change over, a clean down or turnaround, an activity that is a bottleneck or a constraint that affects the process such as capacity, flexibility, lead time, inventory or other business performance measure. | Kaizen | Use the plan, do, check, act approach and to use quantifiable objectives and targets for the improvement activity. |
| Course CostFor further information regarding fees, please contact a member of the Business Team, who will be happy to assist with any enquiries. ProgressionFurther progression can be made through a Level 2 or 3 Diploma in Business Improvement Techniques or alternatively through the Apprenticeship route. |
|
Pathway Group, Fairgate House, 205 Kings Road, Tyseley, Birmingham, B11 2AA | Copyright © 2012 Pathway Group
|
|